Riley Maternity & Newborn Health Center | Part 1
- mgilliam7
- Apr 21, 2022
- 4 min read
Updated: Apr 29, 2022

The Riley Children’s Maternity & Newborn Health Center is designed to provide comprehensive maternity services, offering early intervention and serving both low- and high-risk patients. With the goal of reducing infant mortality in Indiana, the center offers a new model of coordinated care that essentially treats mother and baby as one patient and surrounds them with the medical support they need.
This $142M project was a complete renovation, encompassing all 240,000 square feet of the five-story maternity tower. It centralizes all inpatient childbirth and newborn care previously offered at three downtown IU Health hospitals. Able to accommodate 3,800+ deliveries each year, it now houses the largest number of neonatal intensive care unit (NICU) beds in Indiana.
ERMCO project team members had the opportunity to share stories and answer questions recently as part of an all-employee ERMCO Chat. The ERMCO Chat program is part of ERMCO’s vision to continually improve our delivery practices on all projects.
In this post, we’re sharing some of the discussion related to project challenges, the impact of the COVID-19 pandemic, and why this was a special project for our staff.

THIS WAS AN EXISTING HOSPITAL RENOVATION WITH AREAS THAT STAYED OPERATIONAL THROUGHOUT CONSTRUCTION, WHAT WERE SOME OF THE CHALLENGES? The complete tower renovation presented many challenges, including low ceiling heights, crowded spaces, top-down renovation, and ongoing operations. The use of virtual design and construction (VDC), building information modeling (BIM), room mock-ups, and prefabrication along with thorough planning and a collaborative approach were an important part of the solutions to all of these challenges.
Dave Kessler, Account Manager: Every hospital project is complex. This one was super complex. The biggest challenge was probably the demo. We were demoing from the top down, starting from the fifth floor and proceeding floor by floor. All of the electrical feeders came up from the basement, so we had to start our work in the basement and on the fifth floor at the same time. It required a lot of coordination among the estimating team, the design team, and the field team to make sure that whenever conduit was installed, whether that was now or a month from now or a year from now, that the conduit was able to be installed exactly where it needed to be. And the team did a great job.
Mike Hoover, Project Superintendent: There are so many different systems required in a modern hospital and they are all installed above the ceilings and behind the walls. The distance from the floor to the deck is smaller in an existing hospital than it would be in a new hospital, so you’re trying to fit the same number of systems into a tighter space.

Dave Kessler: The head walls in the patient rooms are a good example of the number of systems required and construction complexity. The head walls are designed for efficiency and usability and they look really nice. Most people don’t realize the amount of work that happens before the head wall panels are installed. Remove those panels and behind them, it's full of conduit – conduit for electrical, systems, fire alarm, nurse call, paging, and med gas.
Abe Hundt, VDC Team Leader: I live in a virtual world; I work on models where everything is digital. Unfortunately, with an existing building, you can’t always rely on existing facility drawings as they may not be up-to-date. We built our project models based on information we were given for the existing hospital. Then we’d go to the job site and measure and find out that the information was inaccurate. We would model conduit going into shafts and then find out some of those shafts were already full or didn't exist anymore.

We had quite a few cases like that. There was continual rework of the model required but we were able to make it work. The ERMCO construction services team used a Trimble Robotic Total Station to precisely locate hangers, cable tray support, and conduit, and to help create detailed installation drawings, identifying conduit elevations and large conduit bends. As much as possible was prefabricated and pre-bent in ERMCO’s fabrication facility. This eliminated guesswork in the field and reduced stress during installation.
CONSTRUCTION STARTED BEFORE THE COVID-19 PANDEMIC, HOW DID THE PANDEMIC IMPACT THIS PROJECT?
Mike Hoover: We were really busy and then COVID hit and just blew everything up. We planned as much as we could for the impact but knew we had to be flexible with our plans. We were in constant communication with our crews, with Messer, and with the other contractors. It really made things difficult but we were able to get through it.
Dave Kessler: We were at the height of the job when COVID started and running close to 80-85 electricians. Within a week, about half that number were showing up. That was the situation for about six months, it was a constant battle but everyone at that time was experiencing labor issues. We worked six, and sometimes seven, days a week in order to maintain schedules and get the job done. Mike Hoover and his foremen’s plans changed on a daily basis. Each morning, they reviewed the available labor force and available expertise and adapted their plans accordingly. The team effort that our labor forces put in when they were up against these challenges, was very impressive – and they provided a good product on schedule!
WHAT MADE THIS PROJECT SPECIAL FOR YOU?
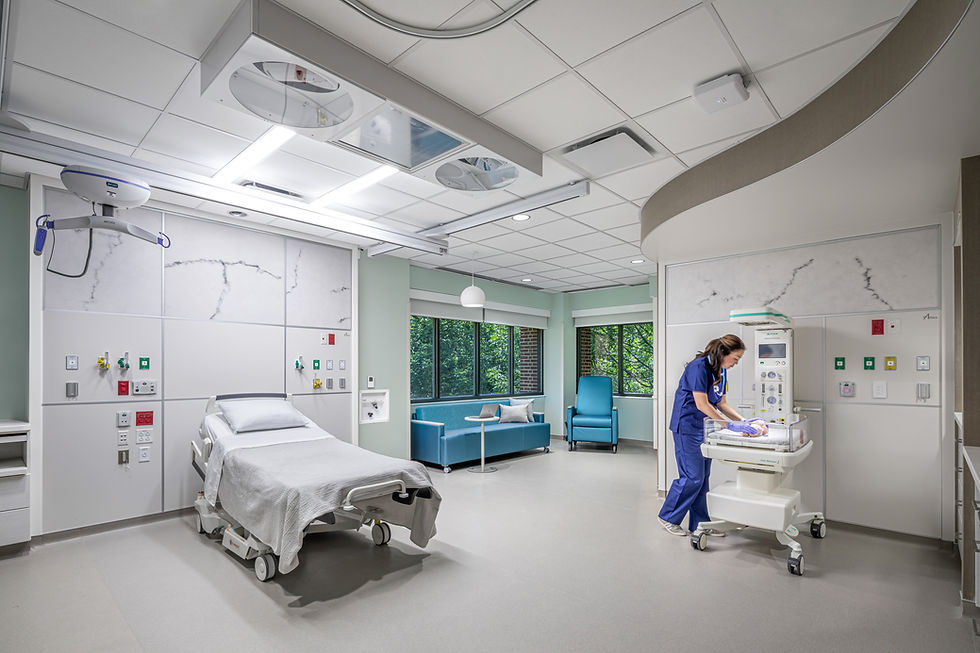
Jon Flanary, Systems Account Manager: Knowing that at some point everyone is going to go to a hospital and knowing that it's been well built and knowing who's built it - knowing your Mike Hoovers are out there doing the work - it makes me feel good.
Abe Hundt: I enjoyed seeing the kids in the lobby, trying to put a smile on their faces, even though they may not be having a good day. I was able to go back with the Ronald McDonald House and serve meals to some of the Riley families. I’m proud to have been part of this project.
Mike Hoover: Maddie Dean is a former Riley patient and a Children's Miracle Network Hospitals Indiana Champion. She toured the project several times. She's been through so much, so it really meant a lot to see and hear from her. This was a special project and visits with Maddie made it even more so for me on a personal level.
CLICK HERE for part two of this blog series to learn about some of the value added services and design assist process.
Commentaires