Innovative, Efficient, and Collaborative: ERMCO's VDC Department
- mbivins27
- Jun 19, 2024
- 3 min read
Updated: Jun 26, 2024
At ERMCO, the Virtual Design and Construction (VDC) department is a cornerstone of innovation, efficiency, and collaboration. With VDC, planning and construction occurs digitally before ground is broken in the real world. We build the project once digitally, visualizing construction flow and working out the big problems, then we’re able to build it more efficiently in the physical world.
Early engagement of stakeholders, which could include the owner, designer, construction manager, and our own field team, allows the VDC team to address potential issues before our work begins on site. VDC moves planning and decision-making earlier in the project process, when it’s easier to make changes that will reduce risk, improve performance, and mitigate cost and schedule overruns. This also helps minimize on-site surprises and foster a culture of innovation and cost-effectiveness.
Field personnel are active participants in the VDC process, providing input on fabrication opportunities and constructability as well as feedback that allows for continuous improvement. This collaboration of virtual design expertise and field installation expertise maximizes schedules, streamlines labor, and enhances job site safety and efficiency.
“VDC BRINGS PEOPLE, PROCESS, AND TECHNOLOGY TOGETHER TO PROVIDE AN INTEGRATED SOLUTION THAT SAVES TIME AND MONEY.” Adam Rude, ERMCO VP Construction Support Operations
ERMCO's Innovations at Broad Ripple Park and IUPUI Innovation Hall
Projects like the Broad Ripple Park Family Center and the IUPUI Innovation Hall are examples of how the integration of VDC and fabrication can positively impact project delivery.
In the case of the Broad Ripple Park Family Center, collaboration between VDC and Fabrication led to the efficient installation of thirty nearly identical exam rooms.

The ERMCO team used a room-in-a-box approach for the repetitive spaces. Each exam room received an “exam-room-in-a-box” with prefabricated electrical items tagged to indicate their specific location within the room. As boxes arrived on site, they were delivered to their designated destination. Electricians removed the tagged items, set them next to their installation location, and then completed the installation quickly and efficiently. This meant we were able to stay on, or ahead of, schedule throughout the project.
The IUPUI Innovation Hall project required innovative solutions to overcome several obstacles including concrete sections poured while electrical and mechanical were still being designed, limited chase space, and confined mechanical room space. The ERMCO team got creative with conduit design and coordination for underground installation. The team designed a frame and used the Trimble tool to precisely identify installation locations for the conduit coming up through the concrete and out of the ground. Locations were marked with stakes and paint, allowing the team to place the frame confidently and accurately. A two-thousand-pound prefabricated pipe rack, constructed offsite, was then set in place and connected to the frame within one day.
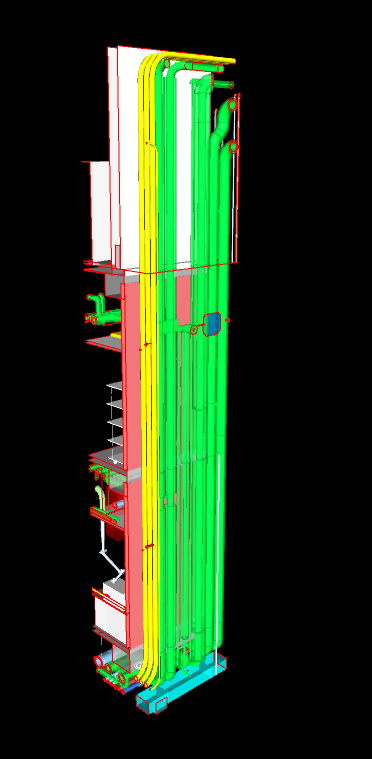
Limited space in a chase running from the first floor to the penthouse made on-site fabrication and installation of electrical and mechanical piping extremely difficult, especially within the time frame desired. ERMCO decided to prefab the conduit and supports that would run through the chase and worked with the mechanical contractor to add it to the prefabbed mechanical pipe frame. The final frame was four stories tall and was lowered into the chase by crane.

This allowed the piping to be fabricated in a controlled environment off site and then installed as one piece. It significantly reduced installation time and eliminated potential safety hazards associated with installation in tight spaces.
The main electrical room on the first floor is surrounded by a mechanical mezzanine, a fire pump room, a stairwell, and a second-floor electrical room. This limited options for routing conduit out of the electrical room to its final destinations. It required innovative thinking and creative design to make the best use of available space while still effectively meeting project requirements.
“THIS WAS THE LONGEST PREFABRICATED PIPE RACK THAT I’VE SEEN ON A PROJECT. I ENJOYED THE CHALLENGE OF COMING UP WITH A SOLUTION THAT WOULD MAKE INSTALLATION EASIER AND SAFER FOR OUR ELECTRICIANS.” Chris Ball, VDC Team Leader, ERMCO
The success of projects like the Broad Ripple Park Family Center and IUPUI Innovation Hall demonstrates ERMCO's commitment to providing innovative solutions to project challenges and providing value to clients.
OR
Contact Adam Rude, Vice President, Construction Support Operations
317.504.5615 | arude@ermco.com
Commenti